Liquid cargo handling equipment
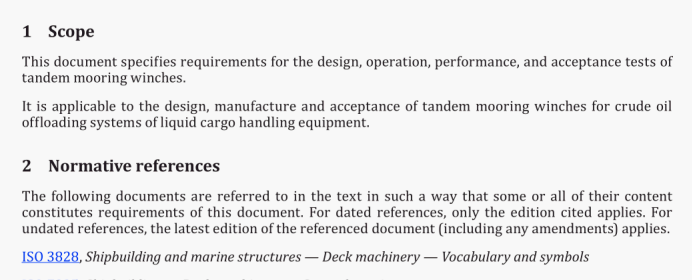
BS ISO 24042:2020 pdf free.Liquid cargo handling equipment—Crude oil offloading system—Tandem mooring winches.
For the purposes of this document, the terms and definitions given in ISO 3828 and the following apply.
ISO and IEC maintain terminological databases for use in standardization at the following addresses:
— ISO Online browsing platform: available at https://www.iso.org/obp
— IEC Electropedia: available at http://www.electropedia.org/
3.1 mooring pull
pulling force from the receiving tanker to the tandem mooring winch during crude oil offloading
3.2 hawser deployment and recovery load
maximum pull of the rope measured at the drum exit as the tandem mooring winch starts to haul or veer at the nominal speed (3,3) with a hawser wound on the drum in a single layer
3.3 nominal speed
maximum rope speed that the tandem mooring winch can maintain when withstanding the hawser deployment and recovery load (32)
3.4 hawser quick release
action of a quick release device to release the mooring hawser quickly with conventional or standby power, aiming to release the excessive mooring pull between the hawser winch and lifting vessel under special conditions, such as extreme sea conditions, so as to disconnect the lifting vessel and guarantee the safety of crude oil offloading.
5.1 General requirements
The design of tandem mooring winches shall meet the requirements of ISO 7825 and 52 to 5fl.
5.2 Material stresses
In accordance with material stresses given in ISO 3730:2012. 4.2 and ISO 7365:2012. 4.1. winch manufacturers shall determine the strength requirements of winch components to enable them to withstand the loads specified in 53,
5.3 Basic calculations
5.3.1 The allowable calculated stress of any affected part under the hawser deployment and recovery load shall not be greater than 0,4 times the upper yield strength of the material.
5.3.2 The allowable calculated stress of any affected part under the safe working load shall not be greater than 90 % the upper yield strength of the material.
5.3.3 In dynamical calculations, the required power of actuators on the drive chain shall not be greater than 80 % the rated power of actuators.
5.3.4 The hawser deployment and recovery load of the tandem mooring winch shall be not more than
33 % of the design breaking load of the hawser when it operates under the corresponding nominal speed.
5.3.5 The safe working load shall be not more than 80 % of the design breaking load of the hawser.
5.4 Drum and hawser
5.4.1 Hawser
5.4.1.1 The hawser is generally composed of a main rope, chafe chains, thimbles, shackles, a messenger rope and buoys. The chafe chains, main rope, thimbles and shackles withstand the mooring pull. The messenger ropes and buoys are mainly used to connect the lifting vessel before the mooring operation.
5.4.1.2 If the quick release device is independent, a chafe chain shall be provided at the head and tail of the main rope. The head chafe chain is used to connect the lifting vessel, while the tail chafe chain is used to connect the quick release device.
5.4.1.3 If the quick release device is integrated into a tandem mooring winch, only head chafe chains rather than tail chafe chains can be configured for the connection of the receiving tanker.
5.4.2 Drum diameter
5.4.2.1 For polyester and polyamide (nylon) hawser main ropes, the diameter of the drum shall be not less than six times the design diameter of the main rope.
5.4.2.2 For polypropylene hawser main ropes, the diameter of the drum shall be not less than four times the design diameter of the main rope.
5.4.3 Drum flange height
When all the rope is reeled on a drum, the flange shall project at least 1,5 times the main rope diameter
above the outermost layer.
5.5 Quick release mechanism
5.5.1 The quick release device can be integrated into the hawser winch or be designed as a relatively independent device. There is no mutual interference between them in terms of functions during use.
5.5.2 After the hawser fully protrudes from the drum and the quick release device withstands the entire mooring pull, the crude oil offloading can be made.
5.5.3 The quick release device shall be able to monitor the mooring pull with a range of 1,1 to 1.3 times that of the safe working load.
5.5.4 When the mooring pull reaches 60 % and 75 % of the safe working load, the tandem mooring winch shall give an alarm signal to remind the operator to observe and decide whether it is necessary to action the hawser quick release.
5.5.5 There shall be an allowable maximum delay of 4 s from the quick release action to the complete release of the mooring hawser.
5.6 Brake
The tandem mooring winch shall be equipped with a drum braking device to prevent the drum from rolling. The braking force shall be able to withstand the hawser deployment and recovery load.
5.7 Operating device
5.7.1 Permanent signs shall be fixed or marked in the direction of movement of the operating device. When the handwheel or the crank cranks the clockwise rotation, or when the handle moves towards the operator, the tandem mooring winch shall recover the hawser.
5.7.2 Unless agreed between the manufacturer and the purchaser, no matter what kind of power source is used, the operating device shall be designed to automatically return to the stop position when the operator releases the controller.
5.8 Auxiliary equipment
The tandem mooring winch can be equipped with automatic or manually controlled hawser sorting devices.
6.1 Test items
6.1.1 No-load test
The tandem mooring winch shall operate continuously for 30 min at no less than the nominal speed.Operate in the forward and reverse directions each for 15 min.
6.1.2 Hawser deployment and recovery test Under the deployment and recovery load of the hawser, the tandem mooring winch shall be continuously operated for 30 min at not less than the nominal speed.
6.1.3 Braking test Each winch shall be equipped with a drum brake device to enable the drum to withstand hawser retraction loads without rotation.
6.1.4 SWL test Apply the SWL on the tandem mooring winch or the independent quick release mechanism for 30 min.There shall be no significant plastic deformation.
NOTE This test can be conducted onboard with agreement between the order owner and the manufacturers.
6.1.5 Quick release function test
Apply 1 % of the SWL on the quick release mechanism for 5 min and then quickly release. The release time shall meet the requirements of 5.5.5.
6.1.6 Full load quick release test
Apply 100 % of the SWL on the quick release mechanism for 5 min and then quickly release. The release time shall meet the requirements of 5.5.5.
NOTE This test can be conducted in factory or onboard.BS ISO 24042 pdf free download.Liquid cargo handling equipment